Calibrating and maintaining thermometers is essential for accuracy and compliance. Key steps include:
- Prepare the calibration environment and allow components to stabilize.
- Choose appropriate calibration methods based on usage.
- Conduct regular maintenance to check for damage and monitor conditions.
- Understand calibration points like the water triple point for precision.
- Keep detailed records of calibration and maintenance activities.
Following these practices guarantees reliable operation. Further insights can enhance your understanding of effective thermometer management.
Key Takeaways
- Ensure a controlled calibration environment, allowing components to reach ambient temperature before calibration to prevent thermal shock.
- Choose an appropriate calibration method based on accuracy needs, considering the thermometer type and operational conditions.
- Regularly inspect thermometers for damage, monitor battery condition, and disinfect before and after use to maintain accuracy and hygiene.
- Document all calibration results and maintenance actions, including dates and adjustments, to ensure traceability and compliance with regulatory standards.
- Preserve calibration records and maintenance logs according to retention policies, ensuring easy access during audits and regular reviews for compliance.
Preparation for Calibration
Effective preparation for thermometer calibration is crucial to guarantee accurate readings and dependable performance. The calibration environment must be carefully controlled; all components, including the thermometer, should reach ambient temperature, generally taking about 15 minutes.
Key steps include:
- Thermometer Inspection: Check for physical damage that may impact thermometer stability.
- Cleanliness: Avoid cleaning the infrared thermometer’s lens unless instructed by the manufacturer.
- Radiation Source Stabilization: Allow the radiation source to stabilize at the desired calibration temperature.
- Avoid Thermal Shock: Begin calibration at lower temperature points to prevent damage.
These preparatory actions guarantee a dependable calibration process, enhancing the overall accuracy of temperature measurements, which is crucial for various applications in scientific and industrial settings.
Choosing the Right Calibration Method
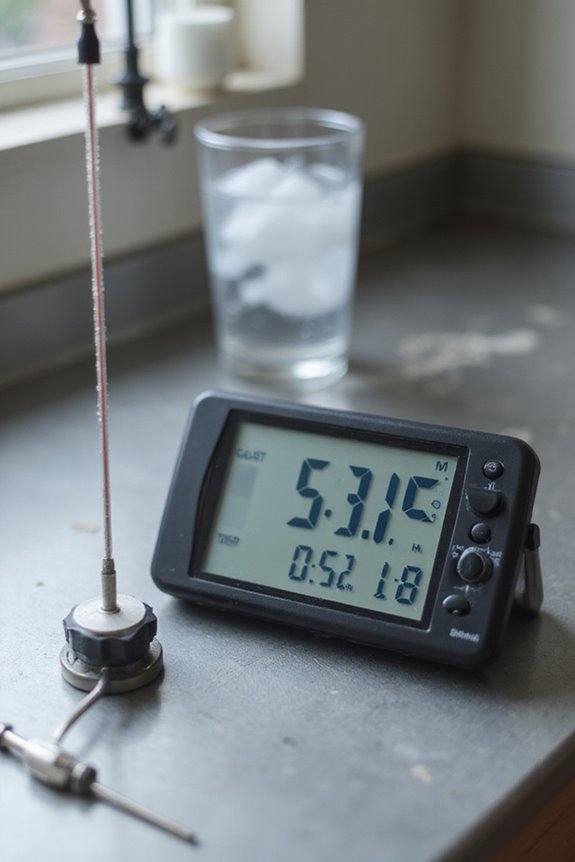
When selecting a calibration method for a thermometer, what factors should be considered to confirm ideal accuracy and reliability?
- Accuracy Needs: Determine the level of precision required for the application.
- Instrument Type: Different thermometers, such as thermocouples and infrared sensors, may necessitate varying methods.
- Operational Conditions: Consider the environment where the thermometer will function.
- Comparison Calibration: This method is accessible, quick, and effective for many sensors, utilizing a high-quality reference thermometer.
- Fixed Point Calibration: While offering exceptional accuracy and reproducibility, this method is complex and requires specialized equipment.
- Professional vs. In-House: High-accuracy applications often benefit from professional services to confirm compliance with industry standards.
Choosing the appropriate method confirms reliable temperature measurements in diverse settings.
Regular Maintenance Practices
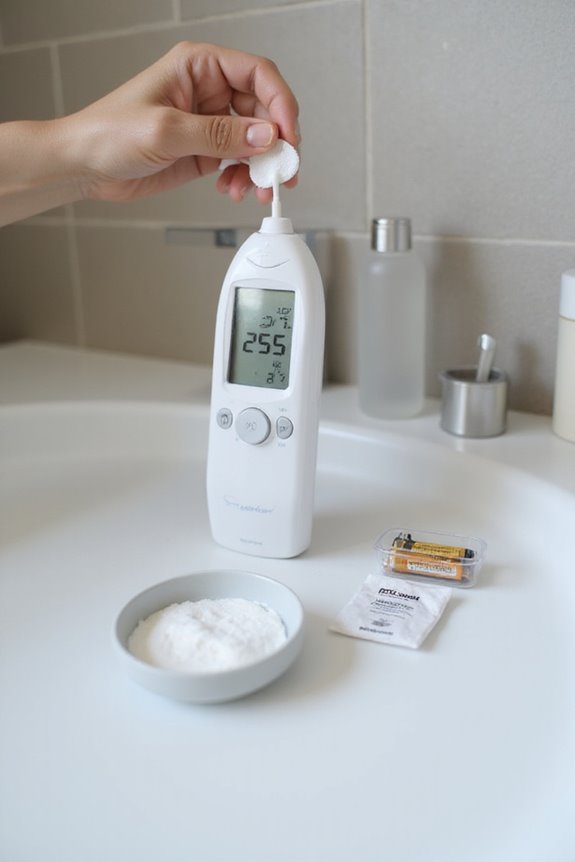
Regular maintenance practices are essential to ensuring the accuracy and longevity of thermometers. Routine inspections should include:
- Visual Checks: Regularly inspect for damage, wear, and corrosion.
- Condensation: Monitor for condensation inside the thermometer’s dial.
- Component Condition: Assess batteries, cables, and sensors.
Cleaning and disinfection practices enhance component longevity. It is vital to:
- Disinfect thermometers before and after each use.
- Avoid harsh chemicals and incorrect water exposure.
- Allow complete air drying post-cleaning.
Documenting maintenance activities provides additional maintenance benefits. Maintain:
- Maintenance Logs: Record all maintenance activities.
- Calibration History: Track calibration dates and results.
Understanding Calibration Points
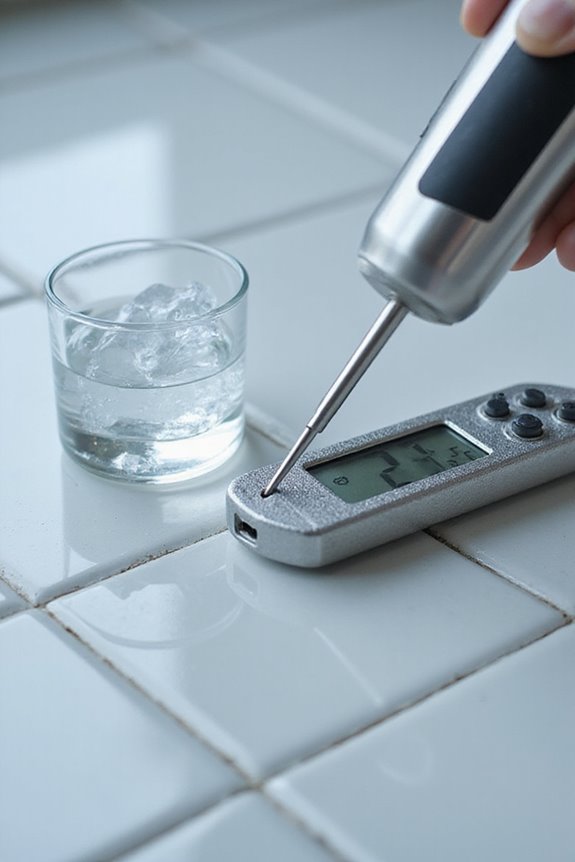
Calibration points play an essential role in guaranteeing thermometer accuracy and reliability. These points are specific temperature references, often fixed points, that allow for precise calibration. Common fixed points include:
- Water Triple Point (0.010°C): The most important fixed point for routine calibration.
- Argon Triple Point (-189.3442°C): Utilized for high-precision instruments.
- Mercury Triple Point (-38.8344°C): Another standard reference.
Calibration accuracy is maximized at these fixed points due to reproducible phase equilibrium conditions. For effective calibration, it is advisable to select at least three points within the thermometer’s operational range. This approach guarantees that the instrument maintains accuracy across various temperatures, supporting consistent performance in practical applications, such as food safety and laboratory settings.
Tools and Equipment Needed
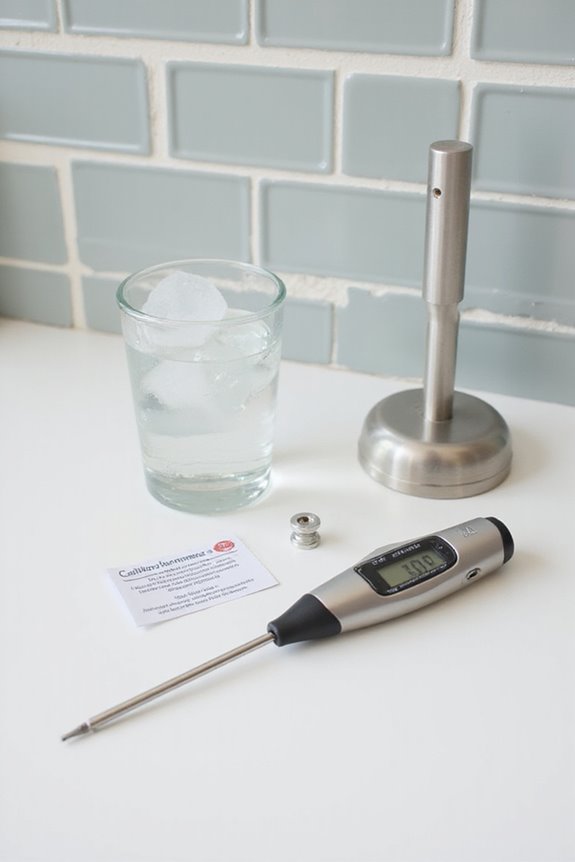
To guarantee accurate thermometer calibration, a range of specialized tools and equipment is essential. The following items are vital:
Calibration Tools:
- Box end wrenches, like the Rhino Thermometer Calibration Tool.
- Temperature-controlled dry-well calibrators for stable calibration.
- Electronic temperature simulators, such as Fluke 714B, for field calibration.
Measurement Instruments:
- Reference thermometers for accuracy comparison.
- Loop calibrators for temperature transmitter calibration.
Calibration Accessories:
- Calibration nuts and adjustment screws for offset corrections.
- Test leads and connectors for sensor compatibility.
- Calibration documentation for traceability.
Investing in these tools guarantees precise calibration, promoting reliability and accuracy in temperature measurement. Understanding and utilizing this equipment fosters a professional approach to thermometer calibration, enhancing collective expertise within the field.
Ensuring Regulatory Compliance
Ensuring compliance with regulatory standards is a fundamental aspect of thermometer calibration. Laboratories must adhere to strict compliance standards, such as ISO 17025, ensuring all calibrations meet high technical requirements.
Key components include:
- FDA Compliance: Essential for companies following Good Laboratory Practices (GLP) or Good Manufacturing Practices (GMP).
- Traceability: Calibration must link back to national or international standards, often through National Metrology Institutes.
- Regular Audits: Laboratories undergo audits to verify adherence to regulatory requirements, including those set by the FDA and HACCP guidelines.
- Documentation: Calibration certificates must detail model numbers, calibration results, and environmental conditions, supporting accountability and traceability.
Continuous quality improvement is vital for maintaining compliance and ensuring accurate thermometer performance across all applications.
Importance of Calibration Frequency
Although the frequency of calibration can vary based on usage and application, it is crucial for maintaining the accuracy and reliability of thermometers.
Calibration Intervals and Accuracy Assurance
- Regular calibration helps detect inaccuracies early, preventing unreliable readings.
- Consistent calibration guarantees repeatable results, minimizing systematic errors.
- Devices used daily require daily calibration; those used weekly may need checks less frequently.
- In critical applications, such as food safety, daily calibration is often mandatory.
- Environmental factors, such as temperature shocks or prolonged storage, can affect accuracy, necessitating checks before use.
- Adhering to manufacturer guidelines fosters compliance and supports audit requirements.
Inspecting and Cleaning Your Thermometer
Maintaining the accuracy of a thermometer extends beyond calibration, necessitating diligent inspection and cleaning practices.
Visual Inspection
A thorough visual inspection is essential. Check for visible damage, cracks, or residue on the thermometer body and probe. Verify the sensor area is free from dust and smudges, particularly for infrared thermometers. Confirm probe integrity, ensuring it is not bent or rusted.
Cleaning Techniques
Utilize appropriate cleaning techniques based on thermometer type. For digital thermometers, use a soft, lint-free cloth with at least 60% isopropyl alcohol. Infrared models require gentle cleaning of the lens and body with a damp cloth. Glass thermometers should be wiped gently, avoiding harsh chemicals. Always follow manufacturer guidelines for best results.
Record Keeping for Calibration and Maintenance
Effective record keeping for calibration and maintenance of thermometers is essential for ensuring accuracy and compliance within various industries. Proper documentation should include:
- Unique identifiers for each thermometer, such as serial numbers.
- Manufacturer details and calibration dates for traceability.
- Calibration results, including compliance statements and uncertainty information.
- Logs of adjustments and maintenance actions, including battery replacements.
Records must adhere to strict record retention policies to preserve historical data for regulatory compliance. Data accessibility is vital; therefore, both electronic and manual logs should be organized for quick retrieval during audits. A designated custodian should oversee the integrity of these records, ensuring they remain up-to-date and accurately reflect the equipment’s performance and maintenance history.
Frequently Asked Questions
How Do I Know When My Thermometer Needs Calibration?
Signs of a thermometer needing calibration often include erratic readings and discrepancies with reliable sources. Calibration frequency may also be prompted by visible damage or inconsistent performance, fostering confidence in accurate temperature measurements for shared environments.
Can I Use Any Water for the Ice Water Method?
When utilizing the ice water calibration method, it is essential to use clean, high-quality water. Impurities and minerals can compromise accuracy, making distilled or deionized water preferable for reliable and consistent calibration results.
What Should I Do if My Thermometer Is Damaged?
When a thermometer is damaged, one must carefully assess repair options or consider replacement. Ensuring safety and functionality, the user should seek professional help, embracing a sense of community in shared experiences and solutions.
How Does Temperature Affect Thermometer Accuracy?
Temperature fluctuations greatly impact thermometer accuracy standards. As devices operate at extremes, sensor stress increases, leading to potential calibration drift and inaccuracies. Regular exposure can compromise reliability, highlighting the importance of understanding these effects for ideal performance.
Are There Specific Brands Known for Better Calibration Accuracy?
Several brands, including Fluke and ThermoWorks, are renowned for their calibration accuracy in digital and infrared thermometers. Their precision and reliability foster trust among users, ensuring consistent performance in both professional and everyday settings.